
Raymond Verhelst & Associates
Global Business Development & Marketing Consultancy
Implementing Automation
The recent trade show Automate 2015 in Chicago, we saw two complementing industries join forces to educate manufacturers about the growing importance of automation in a manufacturing environment. The Association of Advanced Automation co-located itself with ProMat 2015, which is one of the nation’s largest exhibitions on material handling and logistics.
We, as an audience are often amazed by videos of advanced automotive assembly lines where dozens of robots dance a coordinated waltz, welding, assembling and finishing cars. But the associated cost of implementing automation and to the higher level, robotic manufacturing has been considered out of reach to the small, mid-volume producer.
At this show, we actually saw a new class of robotics. Smaller, easily programmed for light manufacturing, and cost effective. As one reporter from ZDNet noted, “Much of the chatter has focused on the obvious: flexible automation technology is now available at a modest price point.”
The emphasis was on filling repetitive positions, sometimes in harsh environments. The message was less about eliminating jobs but facing the reality that there are just some positions that workers are not interested in taking or holding for any length of time.
In relationship to the preceding paragraphs about InSourcing, we talk about the balance of a qualified workforce and manufacturing profitability. During the show, robot producers were conscious of the role their devices play, and talked more about working alongside a higher educated workers who can manage the programming, monitor the output and interrupt when things go wrong. Much like today’s automated CNC milling and processing machines, or 3D printing the associated workforce handle the programming, evaluation of the process and often complete the finishing process.
At under $40,000 dollars, these compact versatile helping hands have a demonstrated payback in as little as 200 days. We used the UR3 from Universal Robotics as an example. The UR3 is a six-axis articulated arm. Each wrist can rotate 360 degrees and the end joint has infinite rotation that can even set screws with a predetermined amount of torque. The arm can be used in pick and place environments, soldering, and finishing.
We also looked at Sawyer, the offering from Rethink Robots. With its screen enabled digital face to show emotion, this single work arm weighs in a just 42lbs. and plugs into a standard wall outlet. The unit offers high-resolution force sensors to gauge the amount of grip and hold-down capacity. There are also 2 cameras that allow the operator to monitor production in great detail. The company claims this unit is perfect for processes like circuit board testing, and material handling. Again, at an estimated price in the low $30k, this has a reasonable payback period.
With more than a dozen companies offering available products or introducing new devices scheduled for release during the year, there were ample solutions to help light manufacturing, sub and final assembly operations control both labor costs and consistent quality.
As for the next generation of a technical or engineering workforce, these are basically dumb devices. They need programming, they need maintenance, they need integration into a larger scheme of manufacturing and eventually, they will need to be upgraded. While they might take away a redundant assembly line position, and that would be challenging to a low-skilled laborer, this is an inevitable process that will allow the growth of InSourcing.
RVA is currently working with a number of clients where sub-assembly, light manufacturing and warehouse, distribution and fulfillment processes are part of the overall business plan.
"Rethink raised 26.6 million from investors such as GE Ventures and Goldman Sachs during the 1st Quarter of 2015 to go global"
"Universal Robotics has US distribution including Position Technologies in Chandler, AZ"
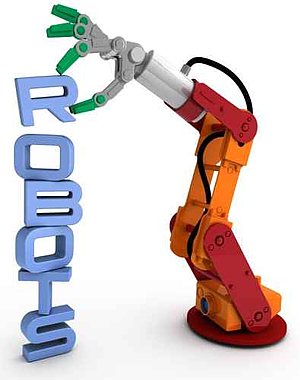
Editorial: InSourcing and the Beneficial Rise of Automation
by Ray Verhelst
As RVA has often been quoted as an unabashed promoter of InSourcing and bringing manufacturing jobs back to North America, we should vocalize our motivations and outline the information we use to justify our enthusiasm. To be fair, as the founder, I also realize there are circumstances where this is not practical, nor profitable for corporations focused on the bottom line.
For most American’s there is a convenient laps in memory when recalling that China has 1.3 billion people, or that India is close behind with 1.2 billion. When compared to North America, where the combined population of Canada and the US equals 354 million, we are but a drop in the bucket in terms of domestic market opportunities. Granted, discretionary income is higher in the US and we are considered a consumption-based economy, but the sheer volume of potential sales in these two growing markets often outweighs the nationalistic cry for bringing companies back on shore.
Why the comparison? For companies that see an opportunity in these countries, manufacturing there makes the most sense. Again, we apply the business philosophy of bringing the manufacturing of goods as close to the market you intend to serve. Shareholders demand that their investments earn profits and require management to seek out growing markets and opportunities.
Jumping back across the pond, we are talking about how to effectively bring back manufacturing, or at least sub or final assembly to North America. We know that the regular increase of cost of living wages in Asia have all but eliminated the labor disparity (at least in China) once thought to dominate the benefits of OutSourcing. In reality, China is now following the same pattern of shipping manufacturing off-shore as well.
In technology and engineering fields, there is much debate over whether we are prepared to fill these growing positions with a qualified and educated workforce. Some push for new educational incentives to attract students into STEM positions. The counter voice claims there are ample engineers and qualified technicians around but they are not interested in working for the current wages.
So we have a dilemma, educating a new workforce from the ground up will take time. Raising wages to meet the requirements of senior technicians may reduce the unemployment lines, but might make the companies and products less competitive. Another reality is that we still need to re-train many of the existing engineers in the new technologies being implemented for today’s fast paced production processes. For this division of workers, there is additional debate over who should actually pay for this education.